Exploring 12 Benefits of Engineered Fastening Solutions
Riveting, stud welding and threaded fasteners
Fastening parts together securely and efficiently is a basic concern in industrial manufacturing, infrastructure, and construction operations. But choosing which type of engineered fastening solution to use on a project can feel overly complicated. Knowing the benefits of each fastening type can make it easy to narrow down your options to the best one.
Three of the most common engineered fastening solutions are riveting, stud welding, and bolting with threaded fasteners. Each offers specific benefits, and in many applications, multiple fasteners will be suitable for a project. In this blog, our Stanley Engineered Fastening experts highlight the top-level benefits of each fastening type, to help give a clear overview of the strengths of each fastener.
Riveting: The Permanent, Practical, And Cost-Efficient Fastening Solution
Benefit 1. Riveting is permanent: tamper and vibration resistant
Rivets provide a smooth, secure fastening solution that cannot be removed easily and stands up to vibrations extremely well.
Benefit 2. Blind rivets can be installed from one side of the application
Blind rivets are named for the ability to install them from one side of a piece without any access to or sight of the opposite side. Advanced riveting technology makes it possible to detect a fault in the deployment of a rivet without visually inspecting a joint.
Benefit 3. Riveting does not damage application panels, therefore can be used to assemble finished (painted) applications
Rivets require neither heat nor mechanical screwing, which means that they can be installed onto panels that are fully painted and sealed without damaging the finish at all.
Benefit 4. Rivets are very quick to install
Rivets can be installed using semi or full automation, or by using lightweight, hand-held tools, making them a cost-effective, rapid fastening solution. They are especially useful in applications where many fasteners are needed on a single panel or the work has to be done in the field.
For applications where two different material types must be joined, access is an issue, or where speed is a concern, riveting is a practical, cost-efficient fastening solution. Avdel riveting tools are air-driven, providing powerful, consistent performance in industrial settings where speed and repeatability are important. The POP and Stanley lines of blind riveting tools offer cordless, battery-powered fastening capacity for hard-to-access applications as well as sites without an available power source. Advanced battery-operated riveting tools perform process monitoring to help minimize errors and track performance.
Stud Welding: Strong, Split-Second Fastening With Limitless Applications
Benefit 5. No hole required for Stud WeldingBeing able to fasten two parts together without drilling a hole helps to maintain the structural integrity of a material, increasing its shear resistance.
Benefit 6. Split-second fastening
Stud welding is extremely fast, which minimizes both the amount of time needed to make a joint and lowers production costs.
Benefit 7. Weld stronger than stud or base material
Because stud welding creates uniform fusion of metal to the base of a fastener, the resulting connection is stronger than the parent metal alone.
Unlike other forms of welding, stud welds can be made by non-certified welders, which means lower labor costs and the potential to cross-train fabricators so that they can deploy multiple types of engineered fasteners.
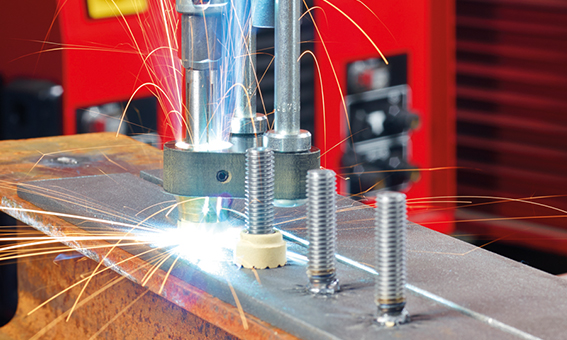
Stud welding offers a reliable, easily installed fastening solution for a range of project types. Nelson stud welding systems provide repeatable welds with process-monitoring capacity to minimize errors. The consistency and controllability of stud welding make it possible for operators who are not certified welders to perform consistent, reliable connections. The Nelson family of arc welders are also available in a wide range of configurations, including cordless electric arc chargers and chargers that can be plugged into a 120 volt home outlet, eliminating the need for a 3-phase power source.
Threaded Fasteners: Versatile Assembly Solutions
Benefit 9. Threaded Fasteners are simple to install and uninstall
Threaded fasteners offer the flexibility to quickly disassemble and reassemble configured elements for moving, shipping, and re-configuring. This is particularly useful in modular systems designed to be expanded and changed over time.
Benefit 10. Variety of sizes and geometries available in Threaded Fasteners
The wide variety of configurations of threaded fasteners makes them suitable for use in many different applications, including those where the thickness of materials makes other fasteners impractical.
Benefit 11. Threaded Fasteners are available in various materials and strength levels
Threaded fasteners are extremely versatile, and can be used to join a wide range of materials such as concrete, metal, and wood.
Benefit 12. Various corrosion-resistant finishes available for Threaded Fasteners
Threaded fasteners offer exceptional corrosion resistance, and varying types of bolts come with finishes suited to specific environmental conditions.
Using threaded fasteners offers secure mechanical connections that can be used for varying material types and thicknesses. The ease of installing and uninstalling threaded fasteners makes bolting an attractive option in applications that are moveable, modular, or where parts will be replaced over time.
In the debate over which fastener is better than another, it is not that one process is superior, but rather that each one offers advantages in specific applications. If you’re having trouble deciding which fastening solution is right for your job, contact one of our specialists to get a recommendation for your project.