3 Ways Battery-Powered Tools are Changing the Manufacturing Game
Cordless electric hand tools are making the manufacturing sector greener, safer, and more cost-efficient.
The manufacturing industry is undergoing a rapid shift as it responds to innovations and growth in the solar, wind, and ground transportation markets. Simultaneously, STANLEY is releasing a new generation of battery-operated, motor-driven hand tools that are comparable to the pneumatic tools traditionally used in manufacturing—especially in engineered fastening applications. Between government initiatives aimed at reducing emissions and consumer demand for more sustainable products, a new era is dawning.
1. Cutting Costs with Cordless Tools
Until now, pneumatic tools were the industry standard in manufacturing, with good reason: they deliver consistent power and require little maintenance. But the inefficient pneumatic systems behind them are costly to maintain, monitor, and operate. Generating compressed air can account for up to 10% of the energy consumption in a production facility, and that doesn’t even begin to address the costs associated with system maintenance and disposal of the oily wastewater byproducts of compressed air. Cordless electric tools also lower the risk for workplace accidents—both from tripping over hoses and being injured by damaged air lines—reducing company liability and the threat of costly legal settlements.
2. Improving User Experiences
In the manufacturing world, technicians use tools in ways that are radically different from the way consumers do. Rather than sporadic use on a weekend project, professional manufacturing teams use their hand tools for hours on end, repeating the same motions over and over. Battery-operated hand tools offer lighter, quieter operation and improved ergonomics over pneumatic tools, partly due to no longer having to “fight” with air hoses. The lower vibrations produced by cordless tools are less physically taxing to operators, and no hoses means fewer trip hazards and no risk of injury from broken or damaged air lines. While the improvements to operator safety are a step forward in the manufacturing industry, this new generation of cordless tools offers another benefit: enhanced quality control features.
Our goal is always to provide the most efficient, reliable, and durable solutions to the challenges our clients face.
— Sean McGain-HardingDirector of Product Management, Global Tools & Automaton at Stanley Engineered Fastening
3. Contributing to a Greener Future
We are entering a period of increased awareness around the environmental impacts of fossil fuel use, and it is driving growth along with policy and regulatory change. Environmental regulations are designed to serve the common good, but compliance can be challenging for production facilities that are required to make expensive upgrades. Shifting from air-driven tools to cordless, electric models is one of the ways that industry is meeting new efficiency standards.
A new generation of fasteners and cordless installation tools have been developed to meet the needs of remote sitework. As demand in the alternative energy generation sector increases, it drives demand for cordless installation tools.
— Sean McGain-HardingDirector of Product Management, Global Tools & Automaton at Stanley Engineered Fastening
Just as global trends have affected the industries mentioned above, the ground transportation industry is also in flux. As battery costs decline and government incentives rise, demand for electric bus and train models is booming. Even the global semi-trailer is shifting to a more sustainable model based on lighter trailer components and optimized logistics. Manufacturers are finding that cordless tools give technicians greater mobility and ease of access around the large-profiles of transportation assembly materials. Unlike tools tethered to an air line, cordless tools give workers greater freedom of movement and offer improved ergonomics.
Newest Members of the STANLEY Cordless Family
As demand for cordless tools in manufacturing reaches an all-time high, STANLEY is continually adding new tools to its cordless line to meet industry needs.
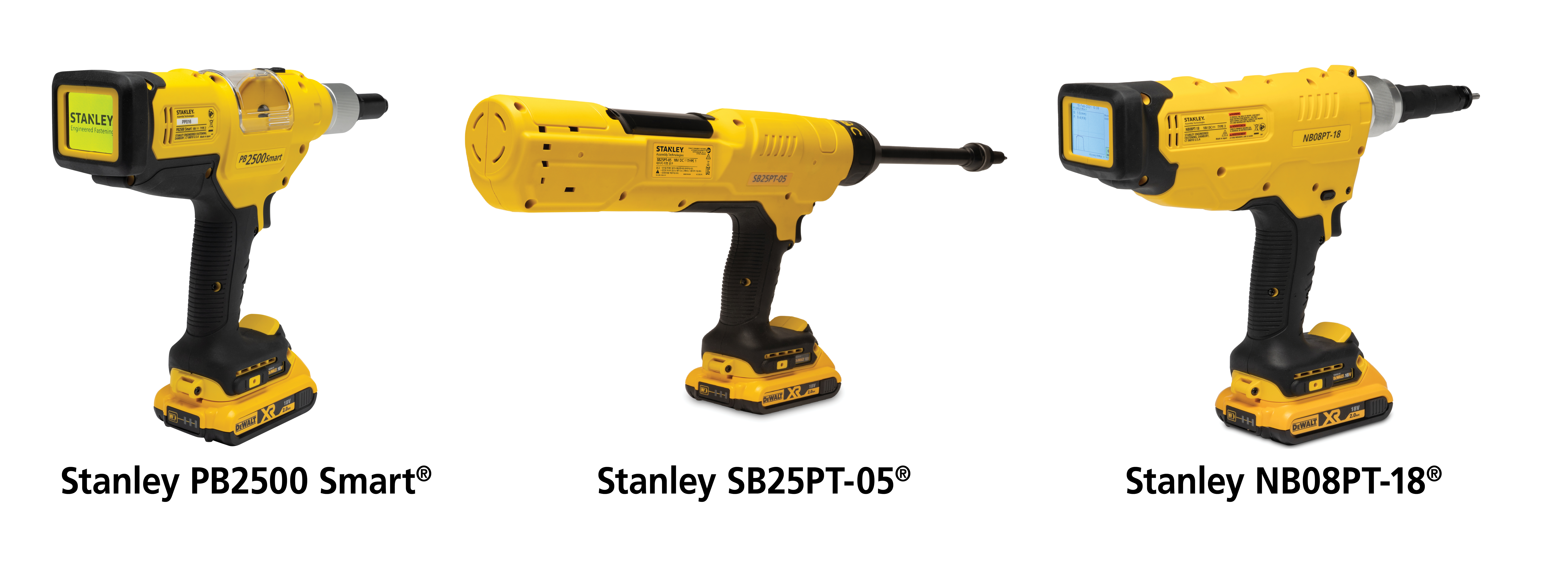
Capable of installing up to 1,100 steel open-end fasteners on a single charge, the Stanley PB2500 Smart® is a blind rivet tool with process monitoring designed for manufacturers in the appliances, bus and coach, solar, and white goods sector. It offers a touchscreen display with rivet counts and other live quality data and is ideal for safety-critical mountings such as seating and handles.
Engineered to maximize efficiency on rail, bus, and coach production lines, the Stanley SB25PT-05® is the first-ever battery-powered speed fastening solution. The speed rivet system is magazine-fed and doesn’t produce any waste material. It is compatible with its pneumatic predecessor tools, allowing easy interchange of components—making the transition to cordless considerably less expensive.
The first cordless blind rivet nut tool in the Stanley Engineered Fastening range, the Stanley NB08PT-18® was designed for bus and rail coach, HVAC systems, and domestic appliance manufacturing operations. It can install 900 steel blind rivet nuts on a single battery charge, features a touch-operated screen with live rivet counts, and has programmable stroke and force settings that provide consistent, precise rivet placements.
STANLEY Engineered Fastening tools continue to deliver increased productivity, sustainability, and safety to the assembly and manufacturing sector while reducing operation costs. This new generation of cordless tools is designed to be “one battery fits all,” meaning that the same DEWALT® battery can operate both a fastening tool and a wide range of other tools, offering flexibility, cost savings, and convenience.