Virtual Control Room Adds Dimension to Data for STANLEY® Warrington Team
Takes factory productivity, feedback, and accountability to infinity and beyond
When Plant General Manager Lee Birchall needs to know the status of any element within the walls of his 176,000-square-foot factory in Warrington, northwest England, making that determination is as easy as consulting two screens mounted in the plant’s conference room.
As the linchpin of the plant's Virtual Control Room, these screens broadcast a wealth of information available in real time regarding every single department involved in the workflow at the Warrington facility, which manufactures single- and two-piece fasteners across multiple product brand lines. The control room, an Industry 4.0 success story and digital manufacturing advance recently implemented by STANLEY® Engineered Fastening, is “the living, breathing hub of the factory,” according to Birchall.
The original concept of a control room was launched at the plant 11 years ago. Then as now, key personnel met twice daily to review the production pulse, identify potential issues and prioritize workload – all with the goal of using data to proactively drive customer satisfaction, leverage efficiencies to control customer costs, and promote creative problem-solving. But the original staging for the numbers on which these meetings were based, was inflexible, and quickly became outmoded. "It was 'a sea of whiteboards,'" says Paul Atherton, Senior HR Manager, STANLEY® Engineered Fastening, UK & Netherlands. “While the meetings were always impactful in terms of teamwork and results, with the previous solution, it was very easy to get lost in all the numbers. Now, it’s much more meaningful.”
The Virtual Control Room provides the opportunity for tailored metrics, real-time monitoring, and positive feedback.—Lee Birchall, General Manager, Warrington Plant
STANLEY® Engineered Fastening
Birchall agrees. “What we wanted in progressing the meetings to digital was to keep the same ethos and deliverables. The Virtual Control Room does just that, while also providing the opportunity for tailored metrics, real-time monitoring, and positive feedback,” he says. “It’s a best practice that aligns with Industry 4.0, the SFS 2.0 pillar of digital excellence, and the SMART factory methodology.”
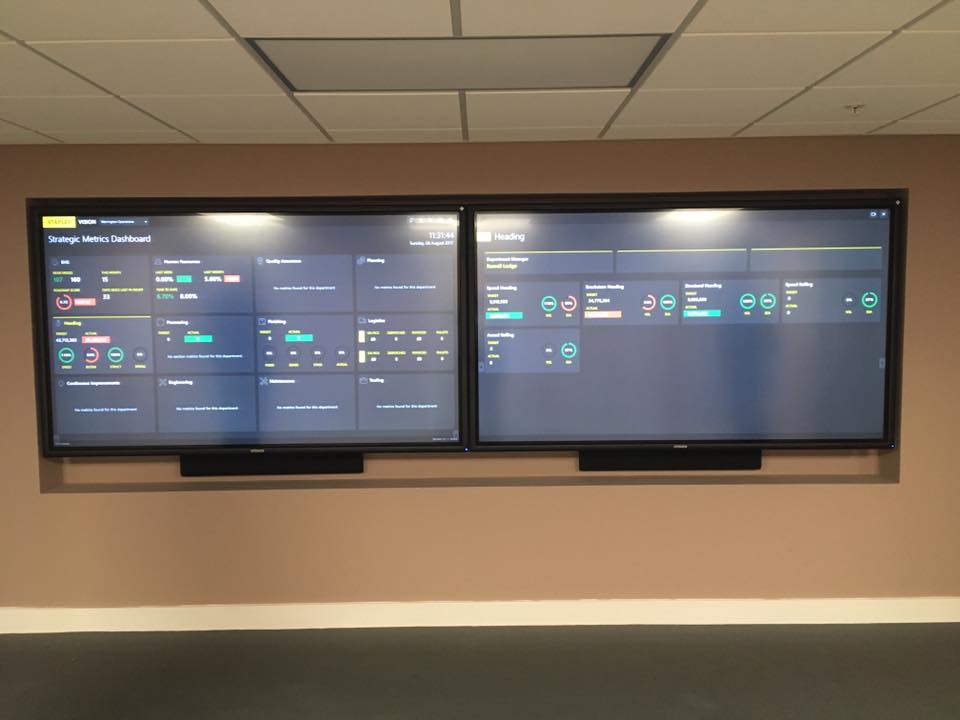
The virtual system, launched in September 2017, integrates all the factory’s essential functions, reporting on not only manufacturing and production statistics, but also health and safety, human resources, and quality. It is also used on an interactive basis for applications like training – for example, the system can be used to administer “Toolbox Talks” to employees, with digital signatures used to record participation and compliance. It provides not only numbers, but extensive data visualization tools, making the metrics easier to take in at a glance. And, there’s no lag time in reporting: personnel throughout the plant use tablet technology to input numbers so that the data is constantly refreshed. All of this equates to Warrington’s quality and output levels constantly reaching new heights: the plant will soon manufacture its 1.1 billionth fastener.
One less easily measurable, but equally impactful benefit of the system is the cross-departmental insight it provides. “For me, this has not only made it much easier to take in the information – you can really experience the data – but it has been an excellent learning opportunity,” says Joann Hepburn, HR Advisor. “From the perspective of someone who’s not working out on the shop floor, the Virtual Control Room gives me more of a window into what other departments are doing. It really makes me feel more like a part of the team."
But the real revelation of the system, according to the department heads, has been the amount of positive feedback that the system enables, thus facilitating creative problem-solving toward the end of meeting and exceeding customer expectations. “Since we work very closely with our software developer, we can take employee suggestions and incorporate them into the system and show results within one to two days,” Birchall says. “But in the 'sea of whiteboards,' this was impossible." Also, everyone on our team is empowered to improve the system. The flexibility of this system provides an extra level of performance.”
You can really experience the data.—Joann Hepburn, HR Advisor, Warrington Plant
STANLEY® Engineered Fastening
How that responsiveness came to be is a testament to the division-wide charge of “Customers, Colleagues, Communities.” The software developer to whom Birchall refers is Ryan Kenny, who started with the company when he was just 15 as part of an unpaid digital data apprenticeship through the local college. Now, as a full-time Business Systems Analyst with the company, Kenny’s software is set to roll out on a global basis through our facilities worldwide.
What’s next for the team? Birchall is excited to introduce the Virtual Control Room to the plant’s employees in totality. At the end of the day, this excitement will undoubtedly translate to even more ideas for performance improvement, thus benefiting the company’s customers. When Lee Birchall adds up all the data on the two screens in his conference room, that’s the final equation: many, many happy customers.
March 30, 2018